Precast concrete has been a cornerstone of modern construction for decades, and in 2025, it’s more important than ever.
With tighter project timelines, rising material costs, and increasing pressure to reduce environmental impact, contractors need a competitive edge. That’s where precast concrete detailing comes in.
By mastering the latest trends, contractors can improve project efficiency, cut costs, and deliver higher-quality results. Think of precast detailing as the secret weapon that bridges the gap between design and construction—making sure every piece fits perfectly, every time.
Key Drivers of Change in the Industry
The precast concrete world isn’t standing still. Here’s what’s pushing it forward:
Economic Pressures: Labor shortages and inflation are driving the need for faster, more cost-effective solutions.
Sustainability Goals: With green building certifications and government mandates on the rise, sustainability is no longer optional.
Technological Advancements: From AI to digital twins, the tools available for precast detailing are more powerful than ever.
Understanding these forces is the first step to staying ahead in 2025.
Top 2025 Trends in Precast Concrete Detailing
Integrated BIM Workflows
Building Information Modeling (BIM) has been around for years, but 2025 is the year contractors fully embrace it for precast projects. Why?
Because BIM workflows streamline everything—from initial design to final installation—saving time and money while reducing errors.
Imagine having a single, unified model that everyone—designers, engineers, contractors, and suppliers—can work from. No more miscommunications or rework.
Plus, the new advancements in BIM Level 3 mean even better collaboration. A recent study found that BIM adoption increases project efficiency by up to 30%.
Visual Idea: A chart showing the rise in BIM adoption rates between 2015 and 2025.
Sustainability-Centric Designs
Sustainability is shaping the future of construction. Precast concrete is naturally sustainable, thanks to its durability and energy efficiency, but the detailing process is where contractors can make a real difference.
Low-carbon concrete mixes, optimized designs to reduce waste, and reusable formwork are leading the way. New regulations, like stricter emissions targets, are accelerating this trend. Contractors who adopt these practices are not only saving the planet but also positioning themselves as leaders in the market.
Case Study: Poundfield Precast’s Ultra-Low Carbon Concrete
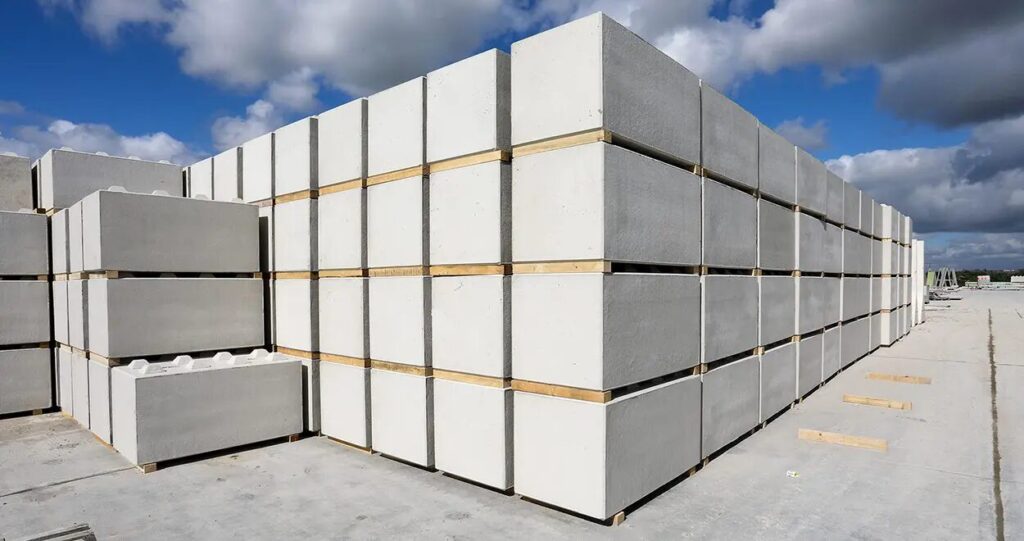
Poundfield Precast is leading the way in sustainability with its ultra-low carbon concrete solutions.
By incorporating innovative methods to significantly reduce carbon emissions, this project highlights how contractors can achieve both environmental and performance goals.
Their approach involves the use of groundbreaking materials and techniques, setting a benchmark for the industry.
Learn more about their efforts here: Poundfield Precast’s Ultra-Low Carbon Concrete.
Automation in Precast Detailing
Gone are the days of manually drawing every detail. In 2025, automation is the name of the game.
Tools powered by AI and machine learning are taking over repetitive tasks like reinforcement detailing and clash detection, freeing up engineers to focus on more strategic work.
Several automation tools and plugins have revolutionized precast detailing, enabling contractors to adapt designs quickly and with greater accuracy. Here are some actionable tips for leveraging these tools effectively:
- Tekla Structures: Ideal for creating highly detailed 3D models of precast elements, including reinforcement detailing and connection details. Use it for precise fabrication-ready models to reduce errors during production.
- Revit Precast Extensions: Great for automating tasks like splitting walls into panels, generating shop drawings, and adding reinforcement automatically. It’s a time-saver for contractors working on modular projects.
- Trimble Connect: A collaboration platform that helps teams share models and track project changes in real-time. This tool is essential for ensuring all stakeholders are on the same page, reducing miscommunications.
- SOFiSTiK Reinforcement Detailing: This plugin for Revit automates the creation of reinforcement schedules and provides detailed 2D documentation directly from 3D models.
By integrating these tools into your workflows, you can improve efficiency, reduce manual errors, and significantly speed up project delivery.
Modular and Prefabricated Systems
Modular construction is booming, and precast concrete is at its core. The precision required for modular systems means precast detailing needs to be flawless. Contractors are now focusing on creating highly detailed shop drawings that leave no room for error.
What’s driving this trend? The demand for faster project delivery and reduced labor costs. Modular systems are pre-assembled off-site and then installed like giant Lego pieces—speeding up construction by up to 50%.
Detailed precast planning is the foundation for success in modular construction. It ensures precision, minimizes waste, and speeds up installation on-site. Without it, projects face delays and cost overruns.
Digital Twins for Precast Structures
If you haven’t heard of digital twins yet, it’s time to pay attention.
These virtual replicas of physical structures allow contractors to monitor, analyze, and optimize their projects in real time. For precast concrete, this means better lifecycle management and fewer surprises during installation.
Digital twins also make predictive maintenance a reality. By analyzing data from the twin, contractors can spot potential issues before they become costly problems.
The ROI on this technology is massive, and early adopters are already seeing the benefits.
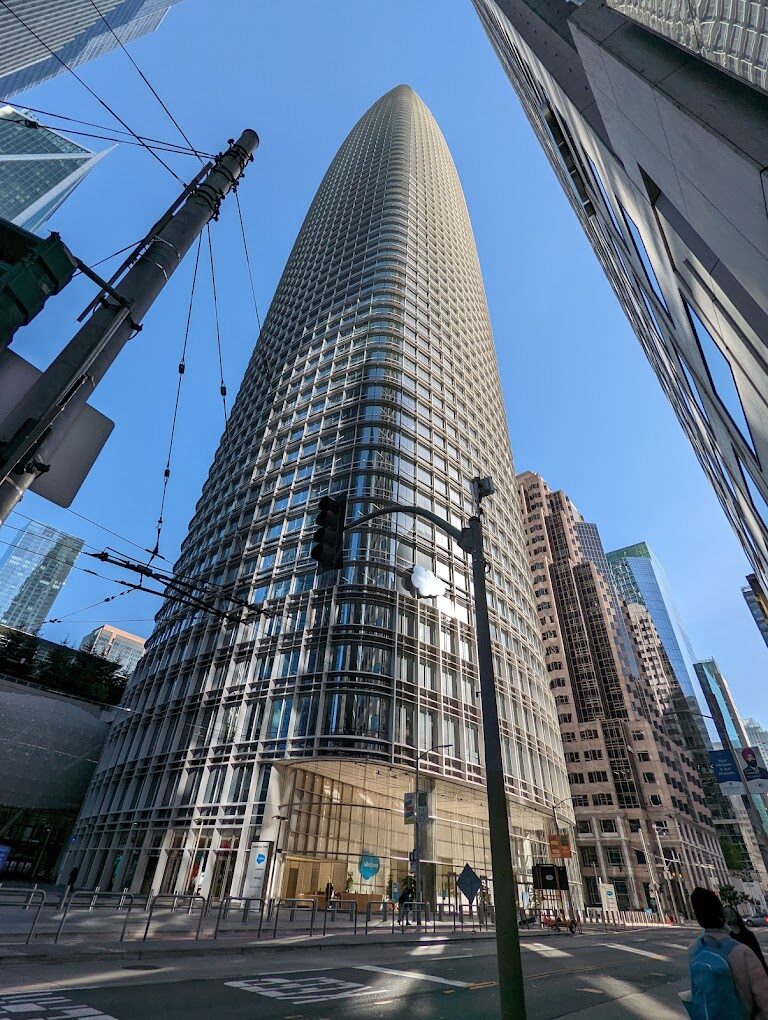
Challenges Contractors Face
Talent Gap in Digital Tools and BIM
One of the biggest hurdles contractors face in 2025 is the talent gap. While the tools for precast detailing are more advanced than ever, not everyone knows how to use them effectively.
The demand for skilled professionals who can navigate BIM software, parametric modeling, and digital twin technology is outpacing supply.
The good news? There are plenty of training programs and resources to help contractors upskill their teams. Investing in training now will pay off in the long run by improving efficiency and reducing costly mistakes.
Navigating Standards and Regulations
Compliance with local and international standards is becoming increasingly complex.
Contractors must ensure their precast detailing meets stringent requirements, from safety codes to sustainability certifications.
Staying informed about these regulations is crucial for avoiding project delays and penalties.
A proactive approach is key. By integrating compliance checks into the design phase—using tools like automated clash detection—contractors can streamline the process and reduce headaches down the line. Here are some tools for clash detection:
BIM 360 Coordinate: A cloud-based platform that offers real-time clash detection and collaboration, enabling teams to resolve issues faster and track their status seamlessly.
Navisworks Manage: A leading tool for clash detection, allowing teams to identify and resolve design conflicts before construction begins. Use it to perform detailed clash analysis on large-scale precast models.
Solibri Model Checker: Excellent for rule-based checking, ensuring compliance with design and regulatory standards while detecting clashes across multiple disciplines.
Implementing these tools can reduce rework, save time, and ensure smoother project delivery. can streamline the process and reduce headaches down the line.
Cost Constraints in Adopting New Technologies
Advanced tools and technologies aren’t cheap.
For many contractors, the upfront investment in automation, BIM, and digital twins can be a tough pill to swallow. However, the long-term benefits often outweigh the initial costs.
One strategy is to start small. Begin by adopting a single tool or process, measure its impact, and scale up from there.
Additionally, consider outsourcing your precast detailing work to specialized firms. This approach allows you to leverage expert skills and advanced tools without the need for significant upfront investment. Many outsourcing partners like Tekance also offer scalable precast detailing solutions tailored to your project needs, helping you meet deadlines and maintain quality standards.
Lastly, look for government incentives or grants that support technology adoption in construction.
Data-Driven Insights
Industry Statistics and Projections
The numbers don’t lie. Precast concrete is on the rise, with global demand projected to grow by USD 174.1 billion by 2025.
Regions like North America and Asia-Pacific are leading the charge, driven by infrastructure investments and urbanization.
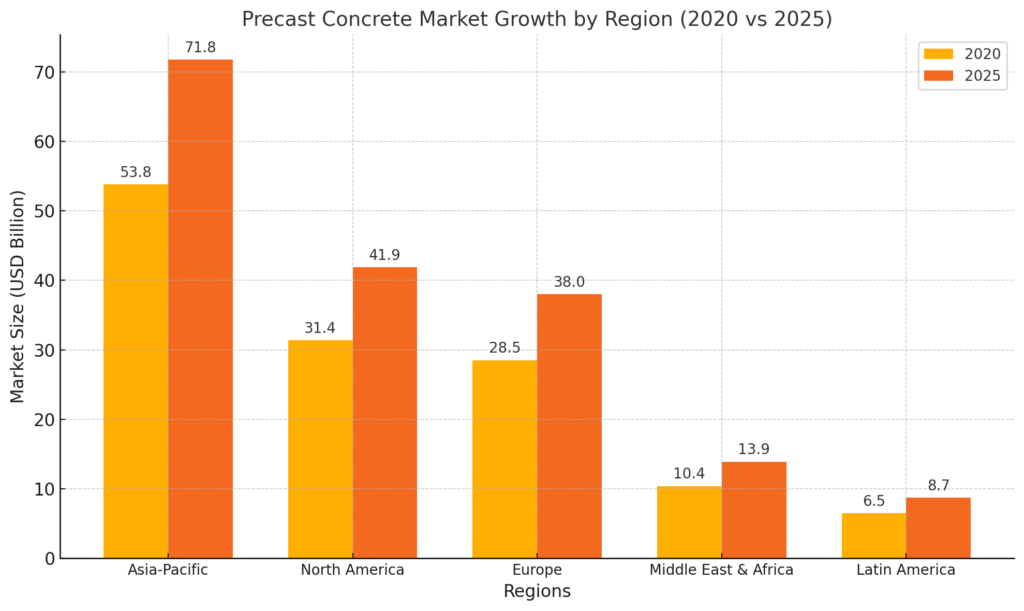
Cost-Benefit Analysis of Emerging Trends
Investing in new trends might seem daunting, but the returns are worth it.
For example, adopting BIM workflows can reduce rework costs by 20%, while automation tools can cut detailing time in half. A side-by-side comparison of traditional versus modern approaches highlights the savings.
Aspect | Traditional Methods | Advanced Methods (e.g., BIM, Automation) |
Setup Time | Longer due to manual processes | Reduced with automation and templates |
Error Rate | Higher due to manual calculations | Lower with clash detection and modeling |
Project Timeline | Extended by rework and miscommunication | Streamlined with real-time collaboration |
Initial Investment | Lower initial cost | Higher upfront costs for tools |
Long-term ROI | Limited by inefficiencies | Higher due to reduced rework and faster delivery |
Sustainability | Challenging to meet green standards | Easier with optimized designs and tools |
Collaboration Efficiency | Limited to manual and offline methods | Enhanced via cloud-based platforms |
Conclusion
The future of precast concrete detailing is bright for contractors willing to adapt.
By staying informed about trends, investing in the right tools, and prioritizing sustainability, you can position your business for long-term success.
These proactive steps will ensure contractors are well-equipped to navigate the future of precast construction successfully.